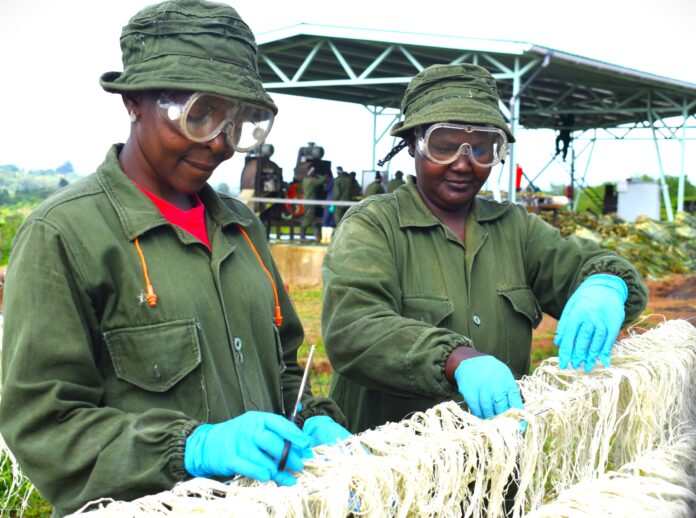
By Lenah Bosibori
Kiambu, Kenya: In the beautiful landscapes of rural Gatuanyaga village located at the heart of Kiambu County in the Central region of Kenya, a remarkable change is happening, as a local firm is transforming waste from pineapples into fibres useful for textile and structural applications, similar to sisal fibers.
Surrounded by endless fields of pineapples, and lush hills where pineapple farming is a way of life, this unique initiative is reshaping the community’s future by providing job opportunities and taking care of the environment.
During my recent visit to the firm, Mananasi Fibre LTD, an organization transforming Pineapple plant Waste into a sustainable revolution in Kenya, I met a group of employees busy working despite the hot afternoon sun. Loyce Nafula is a woman who is employed at the firm despite her physical disability. Nafula shares.
“My main work here is to make pineapple fibre baskets as I can’t stand for long to operate the machines due to my disability,” Nafula shared with Talk Africa.
Nafula adds that she has been tarmacking for so long looking for employment as many employers used to turn her down due to her disability. Luckily, she got one at Mananasi fibre. “I have tarmacked for a long looking for a job around this area which many people turned me down due to my disability but luckily I am happy here at Mananasi fiber,” shared Nafula.
Nafula moved from Kakamega County in western Kenya and got married in the Eastern parts of Kenya due to poverty and high living expenses. She was forced to look for a job and take care of her family.
“Life was extremely difficult because I only depended on my husband who also works as a casual laborer with little income that could not sustain our family of four,” Nafula said while holding fibre bags she had made from her current occupation.
Four months ago, Nafula heard that Mananasi Fibre was opening its doors in the area and she decided to try her luck in employment. Luckily, Nafula was one of the employees picked for the job as a bag maker.
“When I came, I was scared because I didn’t know what I was going to do, I had no idea about machine operation, and due to my disability, I could not stand for long. Luckily I was employed as a fibre basket maker,” added Nafula.
Evelyn Kerongo is another employee who has trained as a machine operator at the firm. She has also been working for two months and she looks forward to more employees getting job opportunities when the company expands.
“I earn 672 Kenya shillings ($4.32) per day, as this is just a start, I am hoping that our boss will increase the figure when the firm gets into full operations,” said Kerongo.
Our boss is a nice person, we have not faced any challenges so far apart from the dust from the machines, we know it is normal but we ensure that we put our protective gear on and take a lot of water and milk so that we are not dehydrated while operating the machines,” adds Kerongo.
Kerongo urges women to take any job opportunity around them and put more effort and energy into learning so that they can be independent and stop relying on their husbands.
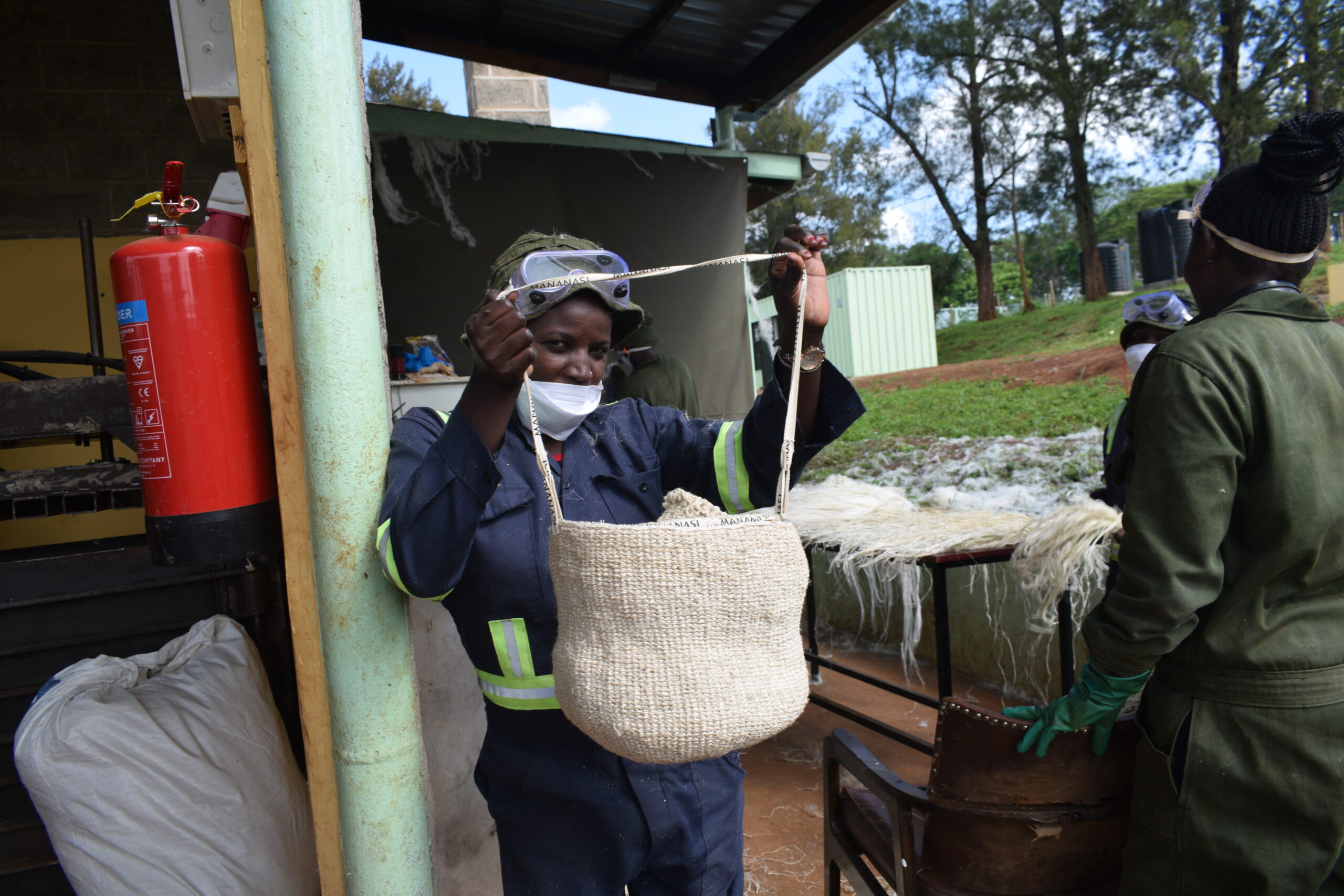
Paul Mwangi is the assistant supervisor at the firm, who has also been working for two months and is looking forward to the company starting full operations so that he can earn more. “We are working hard, and looking forward to huge returns as the work progresses,” he adds.
Located about 60 kilometers from Nairobi’s Central Business District (CBD), Mananasi (Pineapple) Fiber LTD has been in operation for only four months but to a new visitor the firm looks older than the days it has been operating credit to coordination from employees and the founder.
Curious to know more, I met James Boyd-Moss, Founder and Mechanical Engineer at the firm busy repairing machines that kept on crashing down because they were just brought in and were still being fine-tuned for the operations. Moss shares the motive behind the firm.
“When I came here, this place was a kichaka (forest) Moss proudly repeated as he enjoyed my interview in Kiswahili, as you can see, it is now looking like a fully functional factory,” said Moss.
Moss shares with me that it is an idea that came into his mind a year ago since he grew up in a sisal growing area and decided to copy it to his firm.” I grew up on a sisal plantation so I took the sisal concept and applied it to pineapple plant waste,” said Moss.
Currently, the firm which is only four months old has made progress, apart from employing close to 30 people, the firm is looking at building up stocks to send to Ananas Anam an innovative company that repurposes pineapple leaves into sustainable vegan textiles headquarters in London UK with subsidiaries in both the Philippines and Spain.
“We are in the commissioning phase so only producing about 1000kg per month, this should reach 10,000 kgs at full capacity,” added Moss.
In Kenya, about 80,000 tons of pineapple waste is produced monthly. This waste is either eliminated through burning or decomposition, releasing tons of carbon dioxide and methane gas, which are greenhouse gases that contribute to climate change.
Environmental Impact
Moss says that the pineapple leaf fibers used to create the products are from agricultural waste which means that no extra land is required but plenty of water is consumed. The water is also reused as it is put in ponds waiting for a purifier to clean it for further use.
“This production requires a lot of water, currently we get our water from the river through the Delmonte pipes that pass through here. The beauty with our production is that it reduces the amount of pineapple leaves being burnt in the air by reducing carbon emissions from being released into the atmosphere,” said Moss.
Del Monte Kenya Limited is a Kenyan food processing company that deals with the cultivation, production, and canning of pineapple products.
In her remarks during the 8th circular economy conference in Nairobi, Linda Kosgei, the Head of Multilateral Environment Agreements (MEAs) in the Ministry of Environment, Climate Change and Forestry said the government has put in place new policies and legislations to promote sustainable waste management.
“The country’s policy has now shifted from the linear model to the circular model, as we all know, the linear model has been using products without reusing them thus generating a lot of waste,” said Kosgei.
In addition, Casper Edmonds, the head of the Unit for Extractives, Energy, and Manufacturing at the International Labor Organization (ILO) told African journalists in Nairobi during a recent training on the Circular economy that Africa urgently needs to protect those who work in the waste picking industry.
“We urgently need to protect those who work in the circular economy today from the hazards they face, whether through fumes, dust, or chemicals, we need to step up our work,” said Edmonds
While at Mananasi Fibre, Moss has really adhered to Edmond’s remarks as I could clearly see every employee fully protected from the dust, and noise and even gloves to protect their hands from the waste as the photos clearly show.
Data by Kenya Pineapple Industry Outlook 2022-2026 shows that Kenyan consumption of pineapple is expected to reach 284,000 metric tons by 2026, growing at an average of 2.2% year-on-year. This is an increase from the 247,000 metric tons recorded in 2021. Since 2017, demand for pineapple has grown 2.3% year-on-year. In 2021, Kenya ranked 23rd, with Malaysia coming in first with 402,000 metric tons in Johor province alone in 2022. Brazil, India, and the United States followed as number 2 and 3 respectively
The report further says that Kenyan production of pineapple is set to reach 303,660 metric tons by 2026, with an annual growth rate of 0.2%. Since 1966, production has increased 6.2% year-on-year. In 2021, Kenya came in 25th place. The Philippines, Brazil, and China were ranked 2nd, 3rd and 4th respectively.
Extraction
After pineapple harvest, the suitable plant leaves that are left behind are collected in bundles and brought to the firm by a vehicle, the long fibers are extracted using semi-automatic machines, the fibers are then washed and sun-dried and during the rainy season, the fibers are dried in ovens.
The dry fibers go through a purification process to remove any impurities which results in a fluff-like material. They are then taken to the second machine to get the fine fiber that is exported to Ananas Anam, located in London, United Kingdom as raw material for making products like sanitary ware, baby pampers, clothes, shoes and many more.
Waste From The Waste
However, it’s important to note that even in this process, waste is still generated. The challenge now lies in addressing and minimizing the environmental impact of the secondary waste produced during pineapple fibre extraction.
Balancing the benefits of utilizing pineapple waste with the responsible management of byproducts becomes crucial in ensuring a truly sustainable and eco-friendly approach to this innovative venture. This is how Moss manages his waste from waste.
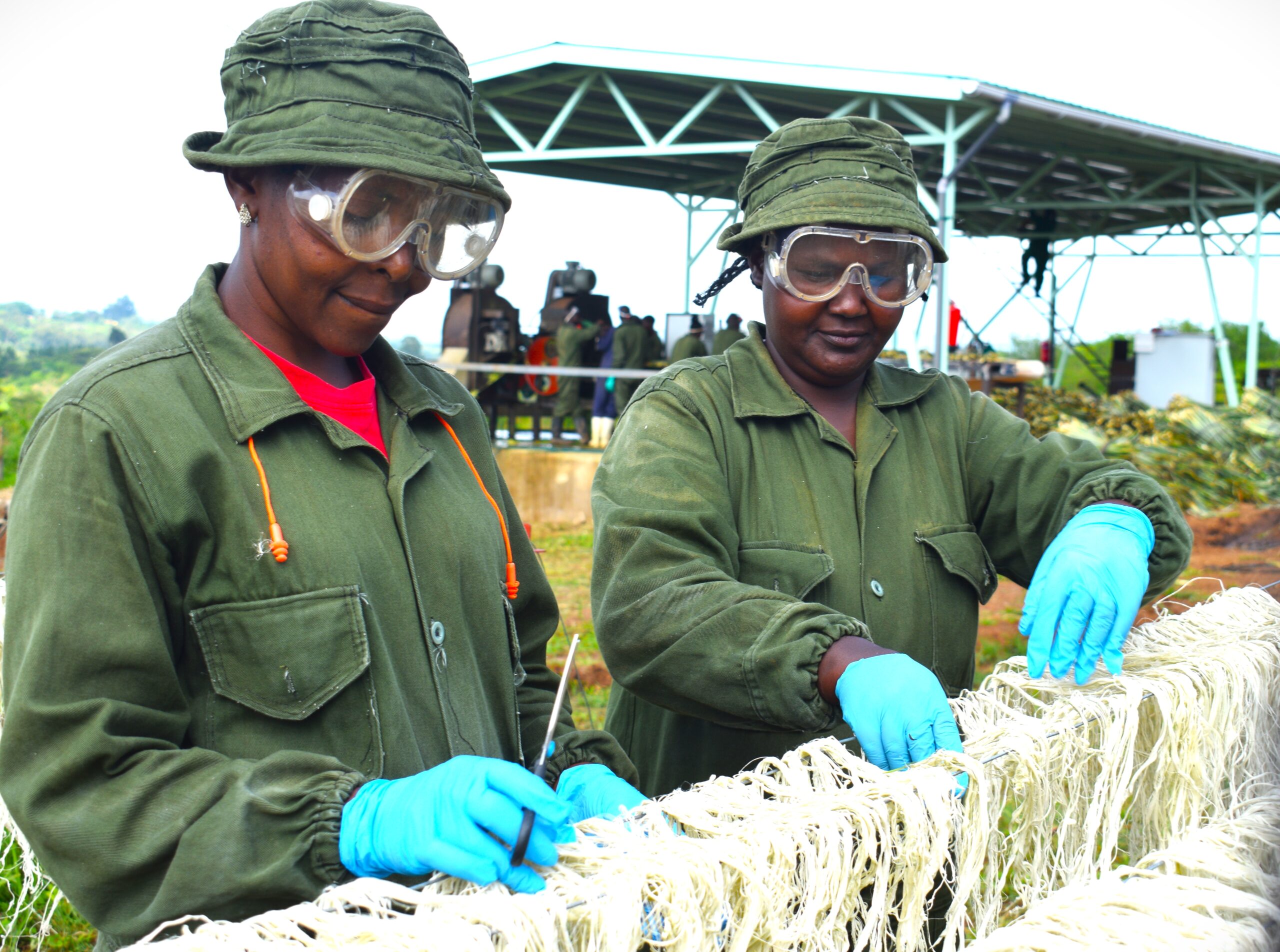
“The idea is to produce organic or compost using the waste from the decortication process and the method that we will be using is aerobic static pile composting so it gets put into big piles with a pipe, feeding the bottom and then periodically you come and blow air down the pipe and that aerates the compost,” said Moss.
At the moment, Moss says that they are commissioning machines and hence no big profit is being realized. “When it will be fully operational, we are hoping to produce 400 kilograms of fiber from the pineapple waste per day (2 shifts),” says Moss.[HP4]
“We will be processing 2,900 tons of raw materials from the field per month, that is the stems, roots, leaves,” he adds.
Currently, Mananasi Fibre relies on the waste from Del Monte but with time he says that the firm will be like an aggregation center for the smallholder farmers to bring their waste and get paid for it. There are ten additional industrial producers of pineapple around here,” said Moss.
“If there are other smallholder farmers that want to commercialize to gain extra value from the plant, they would bring and get paid,” remarked Moss as he checked on the machine that kept on breaking down, as they were still under active development and fine-tuning.
Challenges
Moss says that pineapple leaves are very light as compared to sisal. “Pineapple leaf is like 60 grams and sisal leaf is like 1kg. A very great difference in weight and difference is size and the fiber content for pineapple is small, so the yields from the fiber extraction process are much more than that of sisal,” says Moss.
He says that another challenge is the regular breakdown of machines. “This machine keeps on breaking down. Me and my team of technicians work on the machines together, so maintenance knowledge is disseminated, since a lot of the time I am busy on other parts of the business and not around in the machinery site” adds Moss.
At the moment, the firm has employed close to 30 employees. “I currently have 30 employees and hope to increase them to 160 when the firm will be fully operational if everything goes as planned,” adds Moss.
Mananasi Fibre Limited is sponsored by the Sustainable Manufacturing and Environmental Pollution (SMEP) Programme, a joint initiative by the UK-FCDO and the United Nations Conference on Trade and Development (UNCTAD).